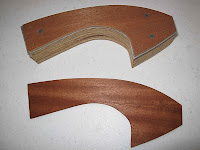
The wings need 104 gussets for the nose portion of the ribs. To make these quickly and uniformly I rough sawed them from the 1/16" 90 degree
mahogany plywood with a
very fine toothed band saw blade. Even my best efforts with the
band saw will not yield uniform parts. Stacking them does not work because the blade wanders more the taller the stack. Instead I used my router to make parts quickly and all within a fine
tolerance. I did this by making a steel pattern, attaching it to a holding block and routing the finished shape with the same formica cutter I use to trim finished ribs.
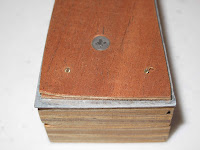
The template is made from 24 gauge galvanized sheet steel from Lowes. I find galvanized steel the best to make templates from. It's cheap (always a recommendation) and easy to work with both in cutting and filing carefully to a scribed line. Steel also holds up well in use as a template. The plywood on top of the template is needed to allow the roller to follow the template and postion the gusset so the blade can cut it.
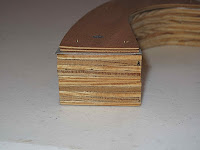
The screw points peeking out from the plywood are there to hold the gusset in place while running the cutter around the template. for this I like the very pointed coarse thread screws like drywall screws. You only need about 1/32" of the sharp tip pointing out to hold the gusset from slipping. I clamped the block in a vise, set the gusset on it and, ran the router quickly around the edge.
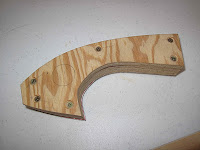
If I were doing it again I would turn the process upside down by drilling a 1-1/4" hole for a vacuum cleaner hose with some air paths out to the screws like in the other block below. You put the block on the hose, set the gusset on and, with the router upside down in a stand run the template around the cutter. It really works slick and quick.