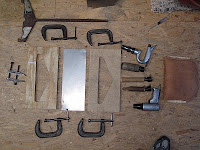
Having figured out how the Elevator and Rudder horns were made, the next task was to form the streamline shaped halves for welding together. We need 6 halves from 20 gauge cold rolled steel. The blanks are cut 16" x 6". I couldn't find small pieces anywhere.
Dillsburg Aeroplane Works used to sell it but got rid of all theirs, probably not a fast mover. The day before our last big snow storm I drove over to Richmond and bought a 4' x 8' sheet. Do the math I have plenty left if someone needs some.
The tools are: form blocks, clamps, air hammer, rivet gun, leather shot bag, 1/2" straight rivet sets, and some hammer tools made from 1-1/4" & 2" dowel. The form block is made 8" x 16" from 5/8" particle board shelving. I made it wider than the blank to give it a little extra strength. The hole was carefully cut and sanded to have nice straight edges and a 1/16" radius for the metal to draw over. Three tools were made from dowel by cutting 6" long pieces and drilling a 1/2" hole 1-1/8" deep with a flat bottom. I thought the dowel would need to be glued to the rivet set but it was a tight fit and as it gets used it warms up and sticks in. Glue might have solved the problem of the hole deepening and the need to cut off the hole end after each part was made. For six parts I just kept cutting them shorter. The 1-1/4" dowel was oak, the 2" poplar. Oak is clearly the right wood since it did not need as much rework. The 2" tool was less than 4" long when I was done but, it never split. I had one of the 1-1/4" tools split along the hole. It was easier to just make a new tool than worry about how to prevent splitting.
The ends of the tools were rounded by hand using the belt sander and some hand sanding with a light casting shadows on the high and low spots. One of the small tools was cut to 3/4" wide to get into the corners. The 2" tool is almost flat on the bottom with about a 1/2" radius on the corner.

I found these vise-grips (made for holding bolt heads) worked perfect for getting the rivet set out of the wood. It really gets stuck tight. They grip without leaving any marks on the shank.
The rings are most of the ends cut off the tools as the rivet set smashed it's way deeper into the wood.
.
.
.
.
.
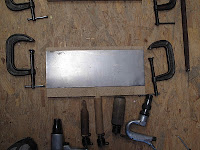
The sheet of steel is clamped between the form block and backing board leaving about 1/2" beyond the trailing edge point. I did all the hammering with the form block setting on the shot bag to reduce noise through the house and prevent damage to whatever was
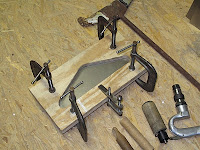
under the clamps. They do not touch the work bench (floor).
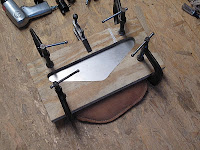
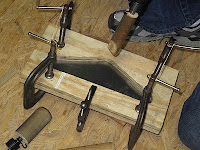
The first tool used is the corner tool. The corners seemed to stretch better if done first. I formed each corner to it's full depth and then used the same tool to form the radius all around the edge.
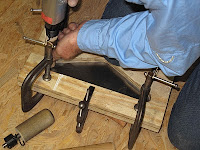
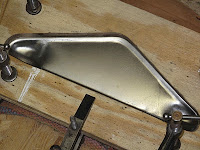
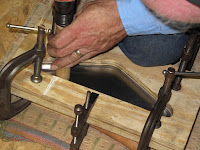
The next step was to use the 1-1/4" round tool to form the leading edge radius. This was blended into the corners to form a smooth transition. The middle part of the trailing edge was left unformed. It takes the least work.
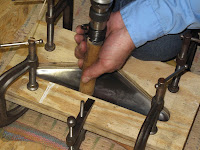
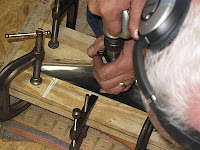
The trailing edge was then formed with the 2" tool to give a nice
streamlined shape. The rivet guns faster rate gives a much smoother finish. The trigger also has better control over speed and force.
Note the noise cancelling head set.
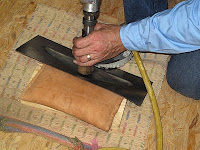
Once the shape looks good and is relatively smooth the part is removed from the form block for some
gentle smoothing with the 2" tool in open areas and the 1-1/4" tool along the edges.
.
.
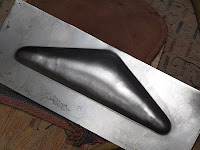
I actually improved this part a little more after taking this picture. The slight
bumps at the left were
easily removed.